Ngành công nghiệp xi măng là một trong những nguồn phát thải khí nhà kính tương đối lớn. Mặc dù khó xác định chính xác lượng khí nhà kính đến từ các nguồn riêng lẻ và so sánh với tổng lượng khí nhà kính, nhưng các ước tính đều đồng ý rằng, ngành công nghiệp xi măng thải ra ít nhất khoảng 5% lượng khí nhà kính (có nhiều nghiên cứu công bố 8%). Điều này khiến cho ngành công nghiệp xi măng trở thành một trong 5 nguồn khí nhà kính hàng đầu và là nguồn phát thải công nghiệp lớn thứ hai sau ngành sản xuất thép.
Xi măng đã được sản xuất như thế nào?
Xi măng portland về cơ bản là xi măng canxi silicat, được sản xuất bằng cách nung đến nóng chảy (nhiệt độ khoảng 1.450 - 1.500°C) hỗn hợp đá vôi và đất sét đã được nghiền mịn. Thành phần hỗn hợp vôi - sét này thường được hiệu chỉnh bằng cách thêm silicat và oxit sắt trước khi được nghiền mịn và đồng nhất.
Xi măng canxi silicat đầu tiên được sản xuất bởi người Hy Lạp và La Mã. Họ đã phát hiện ra rằng tro núi lửa, nếu được nghiền mịn và trộn với vôi và nước, sẽ tạo ra vữa cứng, có khả năng chống chịu mọi hiệu ứng thời tiết. Phản ứng thủy hóa này được gọi là phản ứng puzolan và là cơ sở cho sự đóng góp vào việc phát triển cường độ của bê tông.
Vào giữa thế kỷ thứ 18, John Smeaton đã phát hiện ra rằng một số loại vôi có chứa hàm lượng silica và alumina thích hợp, có đặc tính thủy lực. Nghĩa là chúng chứa canxi silicat và aluminat hoạt tính, có thể phản ứng với nước để tạo ra hydrat bền, có khả năng chống lại tác động của nước. Smeaton đã sử dụng vật liệu này làm vữa xây dùng để xây dựng ngọn Hải đăng Eddystone vào năm 1759.
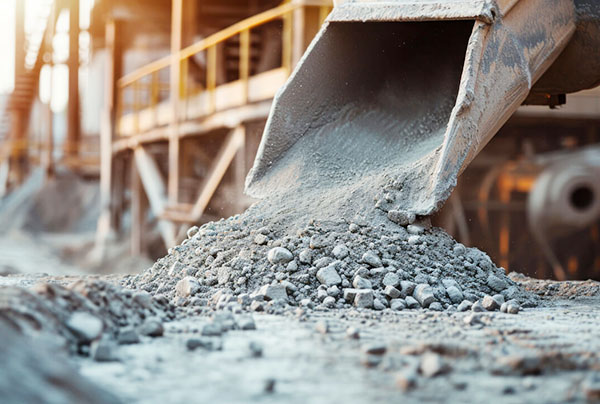
Thuật ngữ "xi măng portland" lần đầu tiên được Joseph Aspdin áp dụng trong Bằng sáng chế Anh Quốc số 5022 (1824), mô tả quy trình sản xuất đá nhân tạo bằng cách trộn vôi với đất sét dưới dạng bùn nhão và nung các cục vật liệu khô đó trong lò nung đứng.
Các quy trình chính liên quan đến quá trình sản xuất xi măng được mô tả như sau: Bước đầu tiên là khai thác nguyên liệu (đá vôi và đất sét) → Nghiền và đồng nhất nguyên liệu thô. Sau đó, quá trình nung nguyên liệu thô diễn ra để thu được canxi oxit (CaCO3 → CaO + CO2), canxi oxit cùng với silica, alumina và oxit sắt tạo thành các hạt gọi là clinker. Cuối cùng, hạt clinker được nghiền mịn cùng, phối trộn với thạch cao và các chất phụ gia hoạt tính khác để sản xuất thành xi măng.
Thuật ngữ "portland" được sử dụng vì sản phẩm sau đông cứng có màu sắc tương đồng với màu đá ở bán đảo Portland thuộc vùng Dorset của Vương Quốc Anh. Joseph Aspdin không phải là người đầu tiên sản xuất xi măng canxi silicat nhưng bằng sáng chế của ông đã được ưu tiên sử dụng thuật ngữ "xi măng portland".
Xi măng được sản xuất trong nửa đầu thế kỷ 19 có thành phần khoáng chất không giống như xi măng portland hiện đại, vì nhiệt độ nung không đủ cao nên không thể tạo thành tricalcium silicate (C3S).
Khoáng chất canxi silicate duy nhất được tạo thành trong lò thời kỳ đó là dicalcium silicate (C2S). Khả năng hoạt hoá và phản ứng thủy lực của khoáng chất C2S thấp hơn nhiều so với khoáng chất C3S.
Clinker xi măng portland chứa 4 khoáng chất, C3S và C2S là hai khoáng chất chính chủ yếu trong clinker (chiếm khoảng 75%), chúng đóng vai trò chính trong việc phát triển cường độ, quyết định các đặc tính về cấu trúc và độ bền lâu dài của xi măng portland. Tuy nhiên, phản ứng giữa CaO (vôi từ đá vôi) và SiO2 (silica từ cát) rất khó thực hiện, ngay cả ở nhiệt độ nung khá cao. Sự kết hợp hóa học được tạo điều kiện thuận lợi rất nhiều nếu có một lượng nhỏ alumina và oxit sắt (thường là 5% Al2O3 và 3% Fe2O3), vì chúng giúp tạo thành pha nóng chảy mà qua đó CaO và SiO2 có thể hòa tan vào pha nóng chảy đó rồi phản ứng với nhau để tạo ra khoáng chất C3S và C2S.
Sự ra đời của lò quay vào cuối thế kỷ 19 và đồng thời đã có những tiến bộ trong công nghệ, cho phép sản xuất ra sản phẩm đồng nhất, nhiệt độ đủ cao liên tục để đảm bảo hình thành lượng đủ lớn khoáng canxi silicat chủ yếu là C3S.
Việc kiểm soát thành phần, chất lượng clinker đã tiến triển từ kiểm soát thử vi sai sang kiểm soát chính xác thành phần hóa bằng các kỹ thuật huỳnh quang tia X, góp phần hoàn thiện công nghệ, tăng năng suất và chất lượng clinker sản xuất.
CO2 đã được hình thành như thế nào trong sản xuất xi măng?
Lượng khí thải carbon dioxide từ quá trình sản xuất xi măng được phân loại từ bốn nguồn chính.
1. Nguồn CO2 lớn nhất từ nguyên liệu chính, do đá vôi được nung nóng và khử cacbon để tạo thành vôi. CO2 có nguồn gốc từ vật liệu đá vôi chiếm tới 50% lượng khí thải.
2. Nguồn CO2 lớn thứ hai là từ nhiên liệu được sử dụng để cung cấp năng lượng nhiệt cần thiết cho quá trình nung luyện clinker. Nhiên liệu chính sử dụng cho quá trình nung luyện clinker xi măng có thể là dầu FO, DO hoặc than đá được nghiền mịn. Nguồn từ nhiên liệu đốt cháy chiếm 40%.
3. Nguồn CO2 từ sử dụng điện chiếm 5%.
4. Phương tiện vận tải chiếm 5%.
Như vậy, các nguồn chính sinh ra carbon dioxide trong sản xuất xi măng là quá trình đốt nhiên liệu hóa thạch và nung vôi. Các loại nhiên liệu phổ biến nhất là than, cốc dầu mỏ, dầu nhiên liệu và khí đốt tự nhiên. Hiện nay, ngành công nghiệp xi măng dựa trên 3 yếu tố cơ bản để lựa chọn nhiên liệu là: chi phí, chất lượng sản phẩm và tác động đến môi trường.
Nhiên liệu đáp ứng tốt nhất ba yêu cầu cơ bản này sẽ là lựa chọn được ưu tiên. Điều quan trọng cần lưu ý là các yếu tố như chi phí cho hệ thống nung mới, lượng lưu trữ và tình trạng sẵn có của nhiên liệu tại địa phương cũng đóng vai trò quan trọng trong quá trình ra quyết định lựa chọn.
Trong quá trình nung trong lò, đá vôi trong nguyên liệu thô sẽ bị phân hủy và CaO, CO2 sẽ được hình thành. Tỷ lệ canxi oxit (CaO) trong clinker thường nằm trong khoảng từ 64 - 67%, phần còn lại bao gồm các oxit sắt, oxit silic và oxit nhôm. Lượng CO2 được tạo ra sẽ bị thay đổi tùy theo hàm lượng đá vôi có trong bột liệu thô.
Một ví dụ về cân bằng khối lượng để sản xuất một tấn clinker xi măng được thể hiện như sau:
Vào lò | Ra lò |
1.530 kg bột liệu | 1.000 kg clinker |
78 kg dầu nhiên liệu | 668 kg CO2 |
1.135 kg không khí cháy | 850 kg N2 |
1,0 kg khí vận/c bột liệu | 226 kg O2 |
Những nguồn phát thải CO2 khác trong nhà máy xi măng, chẳng hạn như từ điện và thiết bị di động, vận chuyển. Tuy nhiên, chúng chỉ chiếm một phần nhỏ (<10%) trong tổng lượng CO2 tạo ra trong quá trình sản xuất clinker xi măng.
(Còn nữa)
Nguồn: Ximang.vn (Văn Vượng - Chuyên gia công nghệ CIDC)